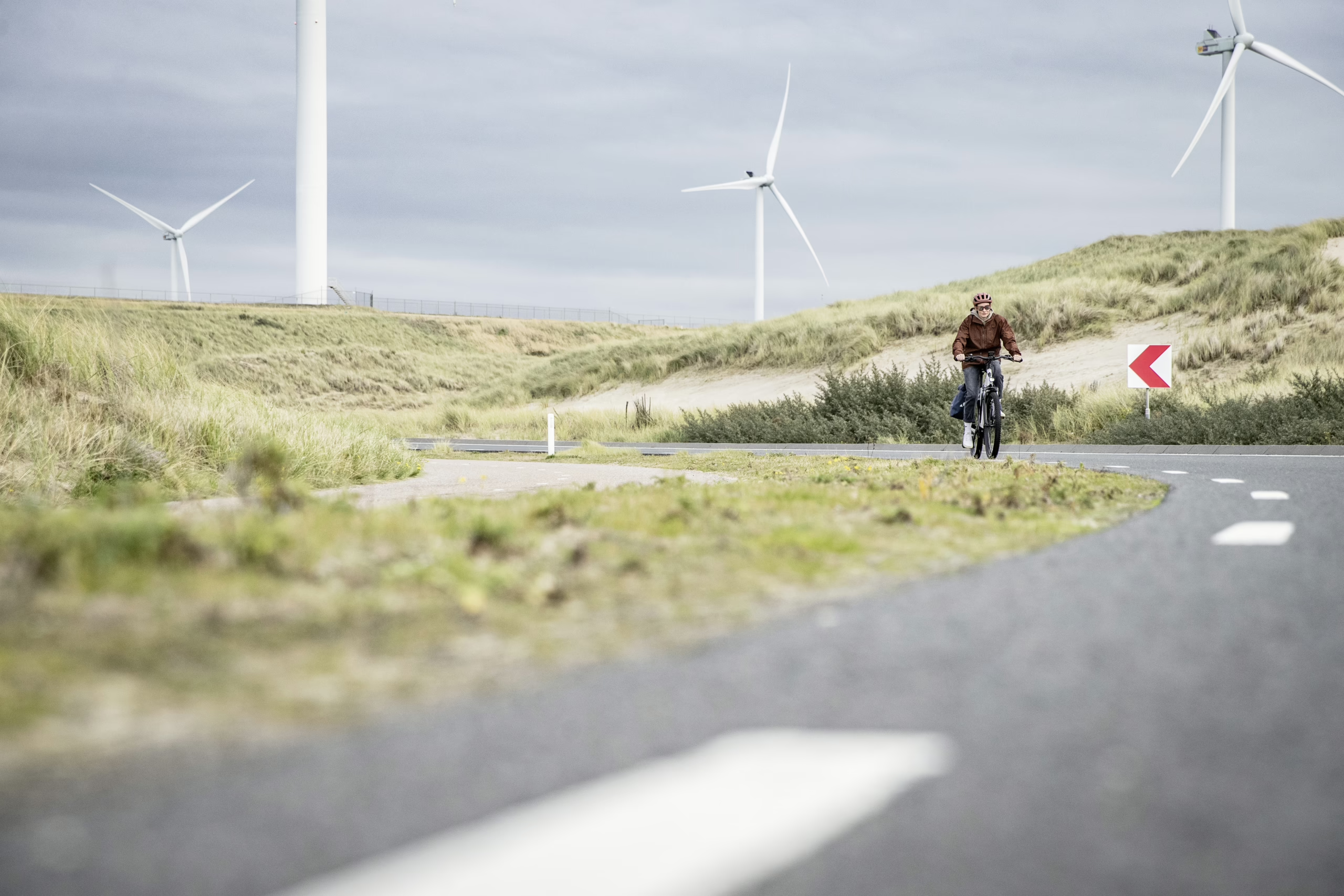
Sustainability at Diamant: A big step with low-impact aluminium
As part of Trek, we are jointly pursuing an ambitious goal: By 2032, we want to reduce emissions in our supply chain by over 30% – based on the base year 2021. An important focus is on aluminium. Aluminium causes about half of the CO2 emissions generated in the production of our bikes and all their parts.
Aluminium in the bicycle industry: Energy guzzler
In a deep emissions audit in 2021, Trek found that aluminium accounts for the largest share of our total greenhouse gas emissions. This is because most of the aluminium we use is produced in plants that run on fossil fuels such as coal, oil or natural gas. This is the standard in the bicycle industry and beyond.
If the same plants were instead to be powered by renewable energies, emissions could be reduced enormously – by more than half. So we want all suppliers of the Diamant factory to work exclusively with renewable energy sources. Trek has conducted extensive research into which electricity is currently used – and of course the result was not always what we had hoped for.
Trek joined forces with the Dutch non-profit organisation Shift Cycling Culture, the German development agency GIZ and other bicycle brands to offer a free online training course for suppliers from Asia. The aim of this training is to reduce emissions through education and to provide basic knowledge on sustainability topics such as carbon accounting, policy development and data analysis.
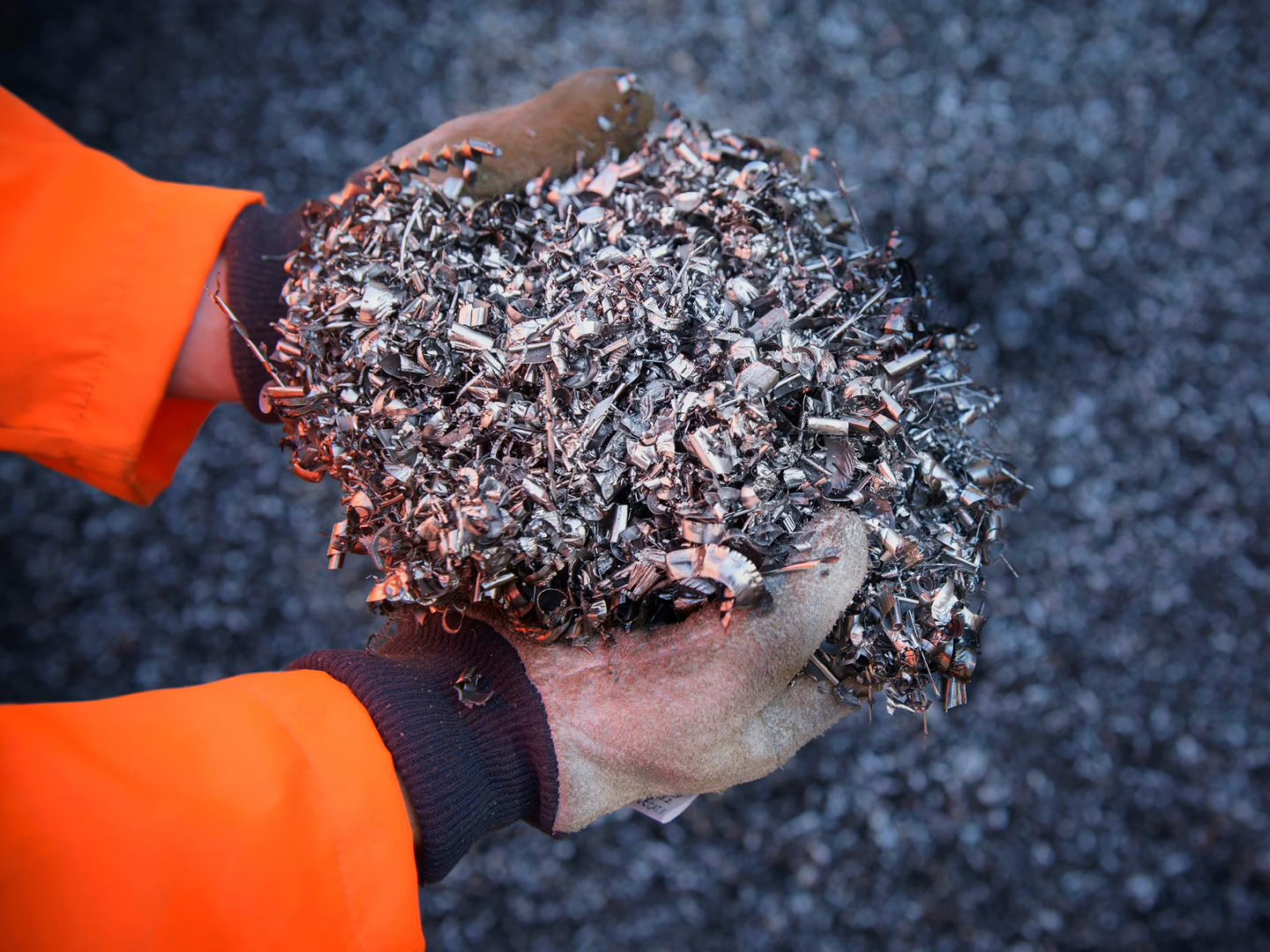
From this information, Trek, and with it Diamant Fahrradwerke, developed a completely new procurement policy for aluminium. This new procurement policy has become the cornerstone of our efforts to reduce carbon. It requires a combination of criteria to be met by our suppliers and that our partners in the supply chain are equally committed.
We have already taken a major step forward with our bicycle frame partner. Hydropower is now being integrated into the production process of our frames as the sole source of energy. This makes aluminium, which we use for our new Zing Gen 3 e-bikes, a groundbreaking material: Low-impact aluminium.
Why low-impact aluminium is so important
The new aluminium reduces emissions in frame production by around 70 percent. This is a huge saving, since frame production alone accounts for 15-25 percent of a bicycle’s total emissions. This makes the Zing Gen 3 models the first diamond bikes on the market – and the first in the entire Trek range – to use this low-carbon aluminium.
What does this mean for the future?
Many manufacturers already rely on renewable energy in their own factories. That’s great. Trek is the first bicycle manufacturer in the world to extend this principle on a large scale to the entire supply chain of frames, parts and accessories – and so are we. With low-impact aluminium, we are taking an important step towards eliminating fossil fuels from the supply chain. But we also know that there is still a lot to be done. Because: The frame is the largest single part of the whole, but it is still only one part of the whole. Our goal is to convert other suppliers and their supply chains to renewable energy as well.
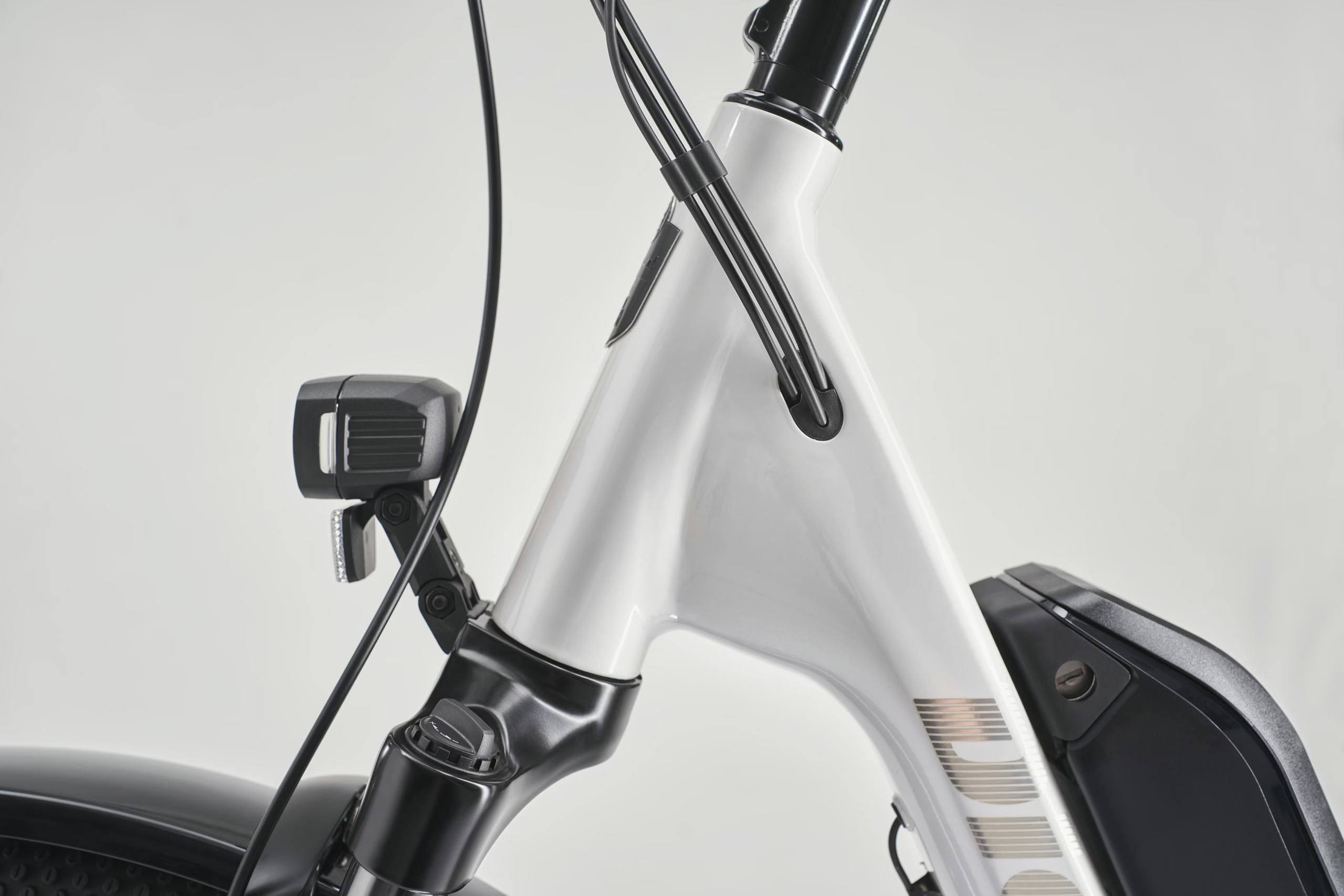
And we are continuing to work on the frame. We are also focusing on future topics such as alternative materials and optimised recycling. Although aluminium can be recycled, it is often contaminated, which reduces its quality. We are working on improving recycling processes and finding more sustainable solutions in the long term.
You can find all the detailed information about our sustainability efforts in our latest sustainability report.